Musicians practice scales before concertos. As an art student I practiced value scales in vine charcoal before attempting to render a sphere. Now in the printmaking domain, I am doing the same thing, only this time I am working with Mark Nelson‘s Precision Digital Negative (PDN) process to calibrate my photopolymer platemaking and printing process.
The goal is to develop a repeatable, end-to-end process starting from the creation of the original artwork, to exposing and developing the plate, through the final printing step. There are many variables that impact contrast, texture, the range of values, the richness of the blacks and the purity of the whites. I want to be able to control each of these variables in order to make the print that I see in my mind’s eye.
The PDN system is a general process for calibrating the production of digital negatives and positives for alternative photographic processes that use ultraviolet light to expose the final image. Mark has put a huge amount of effort into developing and refining the PDN system. His e-book is excellent and chock full of details and explanations of the process itself and related topics like image acquisition and preparation and Photoshop tips. The e-book also comes with membership to a PDN discussion forum where you can get answers to most questions. If you are making digital negatives or positives, I highly recommend purchasing the PDN book.
Creating photopolymer plates for intaglio requires exposure to a positive, rather than a negative. I print my positives onto a transparency film called Pictorico OHP, using an Epson Stylus Pro 3880. I use two types of plates – ready-made SolarPlate and plates I make by laminating ImageOn film to sheets of acrylic. I expose the plates using an old Nuarc 26-1K platemaker that I picked up on Craig’s List.
I’m most of the way through calibrating my SolarPlate process. Once I have the SolarPlate process refined and stabilized, I will repeat the calibration for the more complex ImageOn process.
At a high level, the PDN calibration process involves 4 steps:
- Determine the correct exposure time for clear film.
- Determine the mixture of ink colors in the transparency that yields the ideal density range for exposing the plates.
- Generate a gradient scale using the ideal color mixture
- Generate a set of Photoshop level adjustment curves that linearize the gradient scale.
The photos below document my journey through the initial SolarPlate calibration.
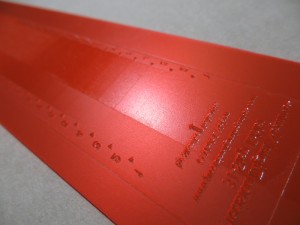
The first step is to determine the correct exposure for clear Pictorico OHP film. One could do this by experimenting with a bunch of different exposure times, but it is much quicker to make a single exposure through a step wedge that incorporates a variety of calibrated neutral densities which simulate shorter exposure times.
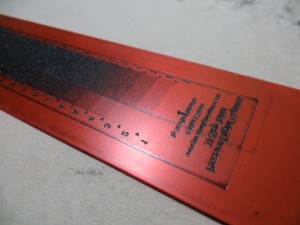
Here’s the step wedge plate, inked, wiped and ready to print. The darker portions of the wedge correspond to darker regions on the plate. Each step in the wedge corresponds to 1/3 f-stop.
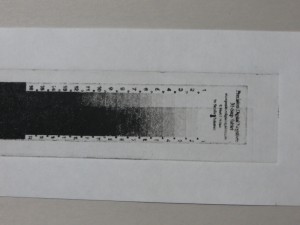
When exposing positives for photopolymer plates, it is important to choose an exposure that just hardens the plate so that it prints pure white in areas where the film is clear. The exposure for this test strip is spot on, but it is apparent that I have a contrast problem because the plate goes from white to black in about four f-stops.
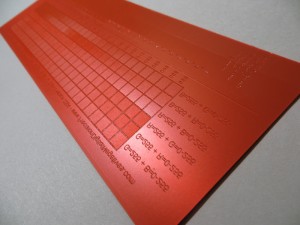
It turns out that black inkjet pigment is not well suited to producing fine tonal gradations in most alternative photographic processes. The problem is the black is just too strong and the printer can’t generate enough different gray values in the narrow range required by the photopolymer plates. Imagine trying to render a figure with a Sharpie and you get the idea. Mark’s insight is that one can choose a mixture of much weaker color inks in order to produce a positive with densities that match the response curves of the plates. By using color inks, it is possible to create hundreds of distinct values across the entire range from white to black. This is a huge improvement over black inks which are so dense they can only create a handful of distinct values in the densities useful for plate making. The squares in the test strip above represent about 150 different color mixtures. The goal is to choose the mixture that just barely yields black.
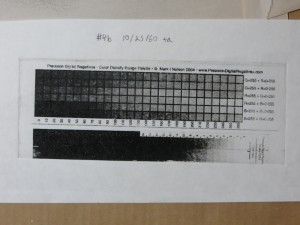
Here’s the color test strip, printed on white paper. Each of the gray boxes corresponds to a different color mixture in the inkjet positive. I chose the forth box from the left in the row labeled B=255 + R=0-255. This box corresponds to a the RGB color R=30, G=0, B=255. This color mixture just barely manages to give me black when it is at maximum intensity. Lighter versions of this color give me lighter shades of gray.
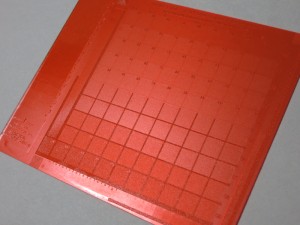
Here’s the plate for the initial gradient scale. This plate was created from a positive that used a mixture of red and blue ink, instead of black. Each square on this plate is a different shade of the RGB color R=30, G=0, B=255.
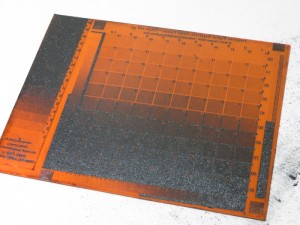
Here’s the initial gradient scale, inked, wiped, and ready to print. Already it is apparent that the plate has a contrast problem – most of the plate is very close to either black or white – only a tiny portion in the middle shows distinct gray levels.
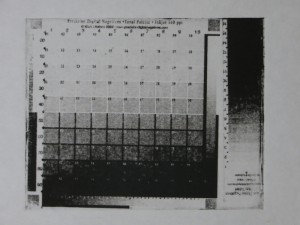
This is the initial gradient scale, printed on white paper and showing 100 different levels from white to black. This scale is not very linear – it is quite flat in the whites, then shoots up quickly to the dark grays and then flattens out again in the blacks.

This plate was created from a new positive which combined the original gradient with the PDN process adjustment curves. The process adjustment curves should linearize the gradient.
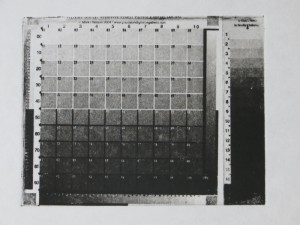
This gradient was produced by applying Photoshop process adjustment curves to the original gradient. This curve is much closer to linear.
Hi Michael, I found your web page wile surfing around.
I recently purchased the PDN and curve calculator from Precision Digital Negatives. It seems very complicated since it’s geared to Palladium printing.
I belong to an intaglio printmaking group in Boston. We recently got a brand new NuArc 26-1ks platemaker.
I noticed that you didn’t use an Aquatint screen for getting the light calibration
When using the 21 step testing. So I’m totally confused and the PDN seems a little to technical. So I’m looking for a starting point. And a simple step by step guide for starting out. As well as printing my positive films in color from a Epson 7800. And using the curve for Toyobo plates.
I realize that this is a big request but any helpful hints would be very appreciative. I’m totally lost.
I wish the PDN gave simple step by step instructions!
Thanks, Steve Miller,
Congratulations on your new platemaker! I will follow up with you offline, but in general, you need some sort of stochastic screen to create the pits on the plate that allow surface tension to hold the ink in place. If you don’t create these pits, the plate will be too smooth, resulting in “open bite” or areas where the ink didn’t adhere to the plate. One way to create the pits is to use two exposures, one with an aquatint screen and a second with the image. Another way to create the pits is to incorporate the stochastic dot pattern into the original artwork. In my step tests I did this by printing with black ink only (no gray) and allowing the printer dithering algorithm to render the gray levels with different densities of small black dots. Both approaches work. The aquatint screen will give you more continuous tones because the dot pattern is higher resolution than the printer can generate, and because the second exposure with the artwork will actually modulates the depth of each pit. When you incorporate the stochastic screen into the artwork, the dot pattern will be at lower resolution and the pits will have all the same depth.
PDN has a bit of a learning curve, but I’ve found it extremely useful. Although the book is directed towards photogravure, Mark Nelson, the creator of PDN does offer workshops on photopolymer gravure. Also, his Yahoo! group for people who have purchased PDN has a lot of great tips for photogravure and Mark is very responsive in this group.
Hi Michel and thank you very much of these really helpful findings of yours. I’m just started to use ImagonHD, learned the hard way to laminate and make a decent exposure using Osram Vitalux -lamp and based on some Capefear Youtube-video, a plastic bag, where the air is sucked with a vacuum cleaner. This “poor man’s vacuum frame” presses the laser transparency positive correctly onto the plate.
I get exactly the same kind of prints you describe using other paper than Stonehenge. I’ve been using Hahnemuhle 703 (730?) damp ,and my prints are like the ones with your’s using Masa. I’ve been thinking of my wiping technique being the culprit, but it can actually be the paper. Using etched zinc plates, there’s no problem with this paper, but perhaps it’s not suitable fior Imagon.
I found here searching for Imagon-wiping actually.
thanks
Matti